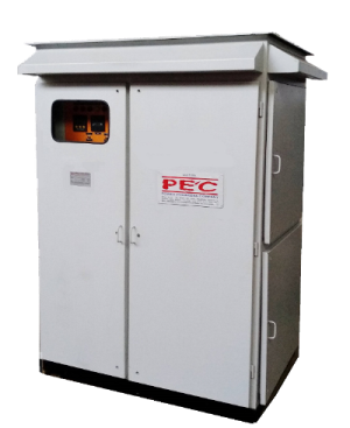

Dry Type Transformer
We are named among the renowned Manufacturers, Exporters and Suppliers of Dry Type Transformer. We offer advanced range of Dry Type VPI /VPE / CAST MOLDED Transformers with off circuit tap links (up to 5000 KVA in 11 KV Class). We use electrolytic grade 99.9% pure copper in the manufacturing process of our Dry Type Transformer. It is basically designed for trouble-free performance, confirming to IEC – 76 & 726. Use of Class ‘F’ / ‘H’ insulation in our Dry Type Transformer increases the heat bearing capacity.
Why Dry Type Transformer From Power Engineers Company (PEC)?
PEC offers advanced range of Dry Type VPI /VPE / CAST MOLDED Transformers with Off Circuit Tap Links (up to 5000 KVA in 3.3 KV Class.), using CRGO M3 to M5 MOH Lamination and Electrolytic Grade 99.9% pure copper. These transformers are designed for trouble-free performance, confirming to IEC – 76 & 726 with low power loss and low noise. Use of modern manufacturing techniques and optimum utilization of active materials ensures cost effectiveness, reliability and a long trouble-free performance.
Dry Type Transformer are fitted in enclosure for Indoor installations and are totally maintenance free and safe from fire as the material used is metal, ceramic, NOMEX and resin. It is environment friendly as there is no oil, hence handling becomes easier and there are no chance of spillages and leakage and there is minimal nontoxic smoke in case of fire. Use of Class ‘F’ / ‘H’ insulation increases the heat bearing capacity and enables the use of the transformer in humid and chemically polluted atmosphere. Fire safety and environmental aspects are of increasing importance. The substitution of oil-filled transformers by dry type transformers is one of the most important steps towards it. VPI transformer is used when it has to be located near load centre and in a fire hazardous place. Special type of fire resistant insulation is used for the windings, thus reducing the fire risk considerably.
Dry-Type Transformers Can have Their Windings Insulated in a Number of Different Ways :
There are several different construction methods used in the manufacture of dry-type transformers, resulting in various designs that make installation in many different environments possible. The key difference in the design of these units is in the insulation of the windings. Dry-type transformers can have their windings insulated in a number of different ways.
- Open wound
The standard dry-type transformer follows a “dip-and-bake construction” method. This is accomplished by preheating the conductor coils and then, when heated, dipping them in varnish at an elevated temperature. The coils are then baked to cure the varnish.
- Vacuum Pressure Impregnation (VPI)
This technique applies the varnish coating in interchanging cycles of pressure and vacuum. The VPI process uses polyester resin. The coils are then cured in an oven. The VPI process is better than the standard dry-type transformer because it includes pressure in addition to vacuum. This process allows better penetration of the varnish in the transformer coil. These units offer an increased resistance to corona.
- Vacuum pressure encapsulated (VPE)
VPE transformer coils are vacuum pressure encapsulated in high temperature Silicone varnish to provide the ultimate protection against moisture. The silicone VPE process utilizes a special four cycle procedure that employs the fundamental principles of vacuum pressure encapsulation and curing. Because of the inherent bonding strength of silicone varnish, the finished coating remains smooth and gives superior environmental protection. Coils receive a minimum of 4 cycles of silicone varnish, and the core and clamping structure are coated with a corrosion resistant sealant that guards against moisture and industrial contaminants. Silicone varnish provides excellent dielectric strength that remains pliable even after thermal aging. The silicone varnish is a true 220 °C insulating material tested to above 250 °C. The silicone VPE process utilizes conventional dry type designs and offers optional conductors, BIL levels, and temperature rises with a 220 °C Class insulation system.
- Cast coil (mould epoxy sealing)
These units incorporate coils encapsulated in epoxy by a moulding process. The transformer coils are solidly cast in resin under a vacuum in a mould. The manufacturing process locks the windings in a strong epoxy resin with high dielectric strength, protecting the transformer from severe operating environments (As mentioned in epoxy cast resin transformer)
Each of the winding insulations noted above is specifically suited for particular environments. Therefore, it’s important to understand where best to use each type. For example, it costs approximately 25% more to specify a cast coil transformer over a VPE or VPI type unit. Therefore, your final selection can have a significant impact on the overall cost of a project.
When improved resistance to corona (i.e., electrical discharges caused by the field intensity exceeding the dielectric strength of the insulation) and increased mechanical strength of the windings are required, you should use a VPI-type transformer.
Use a cast coil transformer when additional coil strength and protection is needed, such as in unforgiving environments like chemical process plants, construction material factories, and for outdoor installations. These types of harsh environments include substances that can devastate the windings of other dry-type transformers, including salt, dust, caustic gases, moisture, and metal particles. Additionally, cast coil transformers have improved abilities to withstand heavy electrical surges, such as recurring but short-duration overloads experienced by transformers serving industrial processes. Cast coil transformers typically have the same increased levels of BIL as oil-filled transformers, while still providing ample protection of the transformer coils. Cast coil transformers are also being used in some harsh locations that were previously thought best served by liquid-filled transformers.
Advantages
- High level of safety.
- No flammable liquids.
- No pollution from leaks solution.
- No toxic off-gasses.
- Can be placed close to the load.
- More efficient.
- Improved reliability.
- Low Noise and low maintenance.
- Easy to repair (open coils).
Specifications
PARAMETERS |
UNIT |
MFG. Detail |
||
Design, Manufacturing & Testing |
|
IEC – 76 & 726. NEMA2 |
||
Name of manufacturer |
|
PEC |
||
Service |
|
INDOOR / OUTDOOR |
||
Transformer Type |
|
Dry Type VPI/VPE/ EPOXY CAST RESIN Transformer |
||
Capacity |
KVA |
UP TO 5000 KVA |
||
Rated frequency |
Hz. |
50/ 60 |
||
Type of Cooling |
|
Air Natural /Air Force |
||
Rated ON LOAD Voltage Ratio |
PRI. Winding |
V |
UPTO 3.3 KV |
|
SEC. Winding |
V |
UPTO 3.3 KV |
||
Vector Group |
|
Dyn/Yyn/ Ynd |
||
Winding Material |
CU |
Copper / Aluminum |
||
Number of Taps |
|
+5% to – 5% @2.5% |
||
Laminations |
CRGO LSSS |
Thickness Less than 0.27 mm ( M3 /M4 Grade ) |
||
Insulation Level |
180°C |
Double Fiber Glass |
||
Terminal Arrangement
|
High Voltage |
|
Cable Box |
Bus Bar |
Low Voltage |
|
Cable Box |
Bus Bar |
|
Detail of Tests in your premises |
Routine test |
|||
IP LEVEL |
IP 45/54 |
|||
Mounting status |
uni – directional wheels |
|||
Ambient Temp. |
50 DEGREE |
|||
Class Of Insulation |
H/F Class |
|||
Guaranteed Over load capacity |
400 % Short Time Over Load |
|||
Provision of Lifting & Jacking Lugs |
YES |
|||
Qty. of Earthing Terminal |
TWO POINTS |
|||
High Resistance Earthed Neutral |
Earth Fault Current Of 5 Amps. |