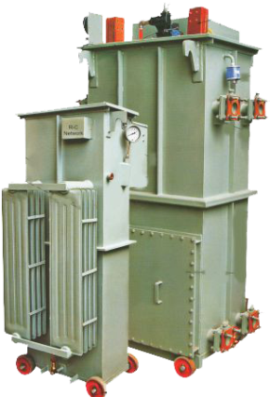

Best Electroplating Rectifier and Anodizing Rectifier Manufacturers and Exporters in Vadodara, Gujarat
Power Engineers Company is a most trusted and leading an electroplating rectifier and anodizing rectifiers manufacturers and exporters in Vadodara, Gujarat. There are numerous electrochemical processes in which electroplating rectifiers can be used, including electroplating, anodizing, hydrogenation, and a variety of other electrochemical processes. Each unit is meticulously tailored to address unique requirements, providing capacities ranging from 500 to 25,000 amps and offering adjustable DC output voltages to meet specific demands.
Electroplating Rectifiers Salient Features :
- Designed for 100% Continuous Duty Cycle
- Compact Design for Space Saving
- Lesser Power Consumption
- Negligible Maintenance
- Tested at Each & Every Stage of Manufacturing
- The equipment is carefully designed with flexibility and undergoes thorough testing to ensure reliable, long-lasting performance without issues.
Electroplating Rectifiers Components :
- OTI
- Oil Pocket
- Oil Level
- Radiators
- Oil Circulation Pump
- Bus Bars
- Siica Gel Breather
- Butterfly Valves
- Earthing Terminals
- Oil Drain Valve
- UNI Directional Wheels
- Window for Diodes
- Oil Tank Indicator
- Lifting Lugs
Electroplating Rectifiers Brief Specifications :
- Input Voltage : A voltage range of 380 to 440 volts, 3-phase, operating at 50 Hz. AC supply or any other voltage
- Output Voltage : The output voltage can either be fixed at a maximum DC level or adjusted variably from zero to the maximum rated voltage.
- Output Current : Rated maximum DC current
- Temperature Rise : Less than 45° C above ambient at the top of the oil
- Efficiency : The efficiency varies based on the voltage and current ratings of the rectifier.
- Ripple Content : Less than 5%
- Insulation : ‘A’ class for oil cooled
Why is regulator control considered superior to thyristor-based control in rectifiers?
- A highly effective regulator is considered the best choice for plating, and the technology has been widely adopted in Germany and Europe for its numerous advantages.
- Many rectifier manufacturers have shifted to using thyristors, largely due to their inability to access the advanced rolling carbon roller regulator technology.
- As a result, thyristor-controlled rectifiers tend to have a lower loss rate than regulators, according to these manufacturers. They often compare thyristors with sliding carbon-type regulators, but in our case, this claim does not hold true. In order to regulate the carbon content, we use a vertical coil-type rolling regulator. The copper section is three times larger, which reduces the losses to about one-sixth, or 20%, of the usual amount.
- With our regulator, the roller moves on both sides of the coil, giving the output of either 440 V or 254 V. A ‘Q’ connection is used on our rectifiers, where the regulator current is only half that of the line current.This reduces energy losses and significantly extends the equipment’s lifespan.
Starting Circuitry: Power rectifiers are designed for 3-phase, 50 Hz operation. A standard AC input supply in India can support voltages between 380 and 440 volts, but custom adjustments can be made to accommodate 60 Hz AC or other voltage specifications. When performing maintenance or in the event of a fault, it is recommended to connect the rectifier input through an appropriate protective device to ensure both personnel and system safety.
DC Output Control:Making changes to the input voltage which is applied to the primary winding of the main transformer adjusts the voltage, current, or operating range of the transformer. The DC output voltage can be smoothly varied from 0 to 100% using an on-load, roller-type voltage regulator.
Advantages of Roller Type Regulator:
- There is no waveform distortion at any load. Electrical waves have the same behavior as moving wheels where their diameters decrease proportionally with the rated voltage, which means that the magnitude of the waves decreases.
- There is an increase in power factor of over 98.
- The cost of spares is very negligible
- There are 3 times as many copper sections for particular currents as conventional makes
- The carbon roller rolls on a coil and lasts more than 20 years without requiring maintenance
- Over all losses are less
Advantages of Conventional Make :
- In thyristor-controlled systems, waveform distortion occurs, resembling a scenario where the wheel is cut by 50% before being set in motion.
- The power factor typically ranges between 0.5 and 0.75.
- The system is highly specialized, requiring the expertise of specially trained electronic engineers for proper repair and maintenance.
- The cost of replacement is very high
- In conventional designs, the copper section used for a specific current is reduced to one-third of the standard requirement.
- Considering the fact that carbon brushes slide on coils, their lifespan is reduced and they break easily
- Over all losses are less