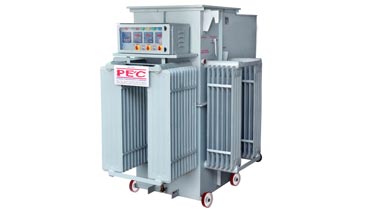

Servo Voltage Stabilizer Exporter, Supplier and Manufacturer in Vadodara
We are a leading servo voltage stabilizer manufacturer, exporter and supplier in Vadodara. Power Engineers Company is Manufacturer, Exporter & Supplier known for reliability and continuous improvement in the field of rolling contact type automatic voltage controller, automatic voltage stabilizer, electroplating, chemical process rectifiers and special purpose transformers. The systems are designed and supervised by a team of qualified engineers having more than 35 years of experience to achieve best possible quality to total customer’s satisfaction.
Introduction :
In spite of best efforts by the State Electricity Boards, the voltage at consumer ends is never the required voltage. This is because of longer distribution lines and different loading at different time on Distribution Transformers. For example, a consumer near the Distribution station gets high Voltage but the farther most consumers may be getting low Volts.
Most of the industries are working in the daytime, so loading on the transformer is more and generally, voltage is low in day time. In the night most of the units are closed and there is practical no domestic load, the voltage may be to the tune of 440-480 Volts.
So, practically every industry needs system which may keep the voltage constant. To maintain the voltage stabilizers are available in the market for refrigerators, electrical machines and electronic equipments but these are of very low capacity. We have developed and installed industrial voltage stabilizer throughout India which are suitable for 100% continuous duty cycle supplied up to 5000 KVA which have more than 99. 5% efficiency.
PEC have developed LINER TYPE REGULATOR WITH ROLLING CONTACT CARBON ROLLERS and installed up to 5000 KVA capacity. Which are suitable for 100% continuous duty cycle & having more than 99% efficiency. Commitment to provide an UNCONDITIONAL GURANTEE for FIVE YEARS. Industrial units achieve the under noted advantages after installing Automatic Voltage Controller.
- Reduction in breakdown of electrical equipments upto 60-80%.
- Energy saving : 5 to 10% on motor load & 15-25% on lighting load.
- Reduction in MDI : Definite reduction in MDI by 10-15%.
- Improvement in power factor : In case of high voltage only.
- Depreciation allowance @ 80% as per Income tax Act
- Uniform quality of end product.
Voltage Optimisation is a term given to the systematic controlled reduction in the voltages received by an energy consumer to reduce energy use, power demand and reactive power demand. While some voltage ‘optimisation’ devices have a fixed voltage adjustment, others electronically regulate the voltage automatically. Voltage optimisation systems are typically installed in series with the mains electrical supply to a building, allowing all its electrical equipment to benefit from an optimised supply.
Over Voltage Various technologies can be used to avoid overvoltage, but it must be done so efficiently so that energy savings resulting from using the correct voltage are not offset by energy wasted within the device used to do so. Reliability is also important, and there are potential problems inherent in running full incoming power through electro-mechanical devices such as automatic voltage controller.
Under Voltage refers to voltage lower than the voltage at which equipment is designed to operate most effectively. If the design of the VO does not take into consideration voltage drop over distance to remote power users, then this may lead to premature equipment failure, failure to start up, increased temperature in the case of motor windings and loss of service.
Effects On Electrical Loads : A common misconception as far as Voltage Optimisation is concerned is to assume that a reduction in voltage will result in an increase in current and therefore constant power. Whilst this is true for certain fixed-power loads, most sites have a diversity of loads that will benefit to a greater or lesser extent with energy savings aggregating across a site as a whole. The benefit to typical equipment at three phase sites is discussed below.
Three Phase Motors : Three phase induction motors are probably the most common type of three phase load and are used in a variety of equipment including refrigeration, pumps, air conditioning, conveyor drives as well as their more obvious applications. The de-rating effects of overvoltage and three phase imbalance on AC motors are well known. Excessive overvoltage results in saturation of the iron core, wasting energy through eddy currents and increased hysteresis losses. Drawing excessive current results in excess heat output due to copper losses. The additional stress of overvoltage on motors will decrease motor lifetime.
Reducing voltage to an induction motor will slightly affect the motor speed as slip will increase, but speed is mainly a function of the supply frequency and the number of poles. Motor efficiency is optimum at reasonable load (typically 75%) and at the designed voltage, and will fall off slightly with small variations either side of this voltage. Larger variations affect efficiency more.
Very lightly loaded motors (<25%) and small motors benefit most from reducing voltage.
If the input voltage of motors driven by Variable Speed Drives is reduced, there will be a proportionate dip in the output voltage and the drive will draw less current and eventually consume less power. However if the motor is running on high load (>80%), the dip in voltage will result in reduced torque and motor will end up drawing more current and power.
Energy Savings : The energy savings achieved by Voltage Optimisation are an aggregation of the improved efficiency of all equipment across a site in response to the improvements in the power quality problems outlined above. It has been and continues to be a key technique for savings in energy consumption. Research in Taiwan suggested that, for an industrial supply, for voltage reduction upstream of the transformer, there is a 0.241% decrease of energy consumption when the voltage is decreased by 1%, and an increase of 0.297% when the voltage is increased by 1%. This assumed a mixture of loads including 7% fluorescent lighting, 0.5% incandescent lighting, 12.5% three phase air conditioners, 5% motors, 22.5% small 3-phase motors, 52.5% large 3-phase motors.
» This higher current affects the electrical motors (particularly smaller capacity motors upto 7.5 H.P.)in three ways :
- Higher current produces higher losses in electrical motors which causes premature failure of winding.
- These higher losses of electric motors also increase the losses of cables, switches, transformers and other associated equipment.
- For smooth continuous operation of motors, over load relays are usually set at 20% higher setting.
REASON OF FAILURE ON MOTOR LOAD : Electrical equipment’s are designed for 230 volts (single phase) or 415 volts (3-phase) and operate with optimum efficiency at its rated voltage. 90% of industrial load consists of motors. Electric motor (particularly smaller capacity motors up to 7.5 H.P.) draws considerably high current at high voltage and increases energy consumption, increases MDI and reduces power factor etc. These excessive power losses of motors generated at higher voltage results in premature failure of electrical equipment’s. Also after the rewinding of motor its efficiency reduced by 3-5% and you have to replace the motor with new one after 2/3 times rewinding.
LIGHTING Within the normal range of supply voltage variations the light output will change by about 3.5% for a 1% change of voltage. The effect of voltage on life is much more pronounced; 5% over-voltage will roughly halve the lamp life, whereas 5% under-voltage will approximately double it. If it is found that lamps are consistently failing prematurely then the first thing to investigate is the agreement between the voltage marked on the lamp, and the actual voltage at the supply terminals. In certain cases, it might seem attractive to operate 230V lamps on a 220V circuit to secure the increased lamp life, until it is realised that in doing so the light output will not fall considerably. It is generally unwise to operate a lamp at anything other than its design voltage, but there are some exceptions. For instance under-volting can be justified for aircraft obstruction lights at the top of a tower where the cost of replacement is very high. By contrast, over-volting is regularly practised in studio lighting, where the extra light output permits fewer projectors on simpler mounting structures and this is a worthwhile exchange for renewing lamps before each filming session rather than after, say, a year of service. The Figure shows the relation between supply voltage variation and the performance of gas-filled lamps. It applies only approximately to vacuum lamps and to tungsten-halogen types.
REASON OF FAILURE ON LIGHTING LOAD : Similar is the case with bulbs and tubes, when voltage increases above 230 volts. For example, at 270 volts, the power consumption of 60W bulb increases by almost 40% and the life of bulb reduce from normal 1000 Hours to 100 Hours only as explained in broacher.
Effect of Voltage On Small Motors
Operating Characteristic |
Effect of Voltage Change On Small Motor | ||
90% voltage |
110% voltage |
120% voltage |
|
Starting and maximum running torque |
Decrease 19% |
Increase 21% |
Increase 44% |
Synchronous speed |
No change |
No change |
No change |
Percent slip |
Increase 23% |
Decrease 17% |
Decrease 30% |
Full-load speed |
Decrease 1% |
Increase 1% |
Increase 1% |
Starting current |
Decrease 10-12% |
Increase 10-12% |
Increase 25% |
Magnetic noise, any load |
Decrease slightly |
Increase slightly |
Noticeable increase |
Efficiency |
|
|
|
Full load |
Increase 0.5-1% |
Decrease 1—4% |
Decrease 7-10% |
3/4 load |
Increase 1—2% |
Decrease 2-5% |
Decrease 6—12% |
1/2 load |
Increase 2-4% |
Decrease 4-7% |
Decrease 14-18% |
Power factor |
Increase 8-10% |
Decrease 10—15% |
Decrease 10-30% |
Full-load current |
Increase 1—5% |
Increase 2-11% |
Increase 15—35% |
Temperature rise at full load |
Increase6—12% |
Increase 4 -23% |
Increase 30 – 80% |
Details
The table below compares the behaviour of 60 watt lamp at different voltage :
Voltage
|
Current
|
Watts
|
Luminous Intensity
|
LIFE IN HOURS
|
220
|
0.25
|
54 W
|
690
|
2000
|
230
|
0.26
|
60 W
|
710
|
1000
|
240
|
0.27
|
65 W-8.3% More
|
820
|
575
|
250
|
0.28
|
70.6-17.6% More
|
943
|
338
|
260
|
0.29
|
75.4-25.6% More
|
1073
|
200
|
270
|
0.31
|
83.4-39% More
|
1213
|
100
|